PREVENTIVE MAINTENANCE
Preventive maintenance models can be used to detect and prevent any kind of hardware failure inside a production process, as long as there are some sensors measuring temperature, pressure, flow, vibrations, speed, etc.
Submersible oil pump failure prediction
The objective was to predict the failure of submersible oil pumps in Russia. In a single area, there were already 500 pump failures per year. The idle-time could reaches 6 months in case of a serious accident. The characteristics of the problem were:
- 5000 wells to manage
- 50 GB of raw data
- Historical depth of 3 years
There were more than 500 variables available from different sensors inside the wells (temperature, pressure, oil flow, etc at various points). We created additional variables to encode the dispersion, the increments and the recency of the different events. In the end, we had more than 2000 variables.
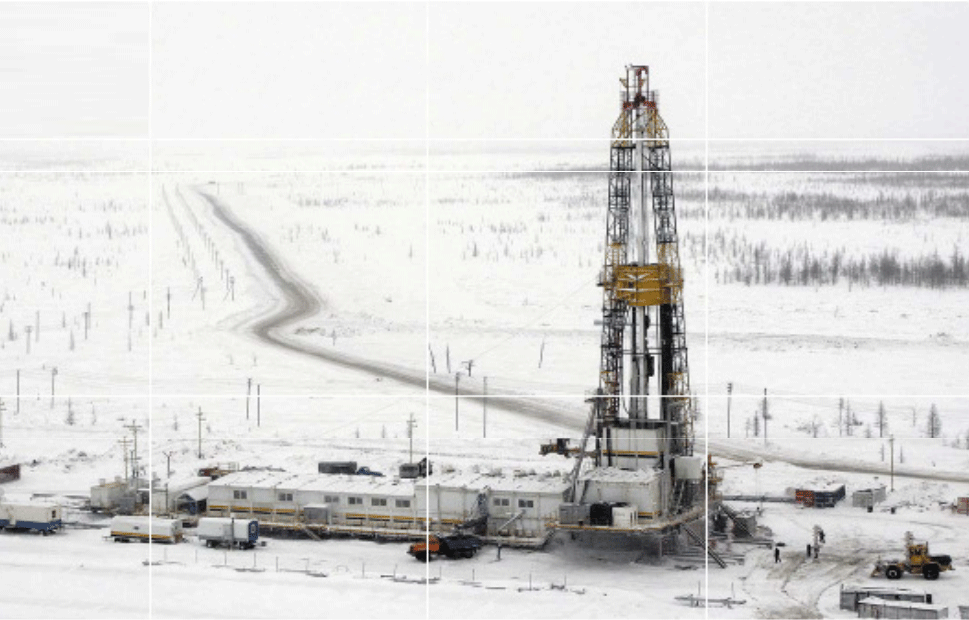
Final results
Thanks to the prediction, we could significantly reduce the plant downtime and manage resources more efficiently.
If we assume that we have 3 out of 10 pumps that are going to fail, the model gave a correct prediction for 70% of them.
Financial results
The estimated financial effects of this preventive maintenance system was:
Reduction of the repair costs: 1.5 billion rubles/year.
Increase of oil production: 1 billion ruble/year additional revenue.
Estimated total revenue: 2.5 billion rubles/year = 31.8 million €/year
ENERGY CUSTOMERS

Enel
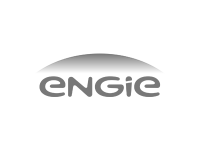